Pultrusion
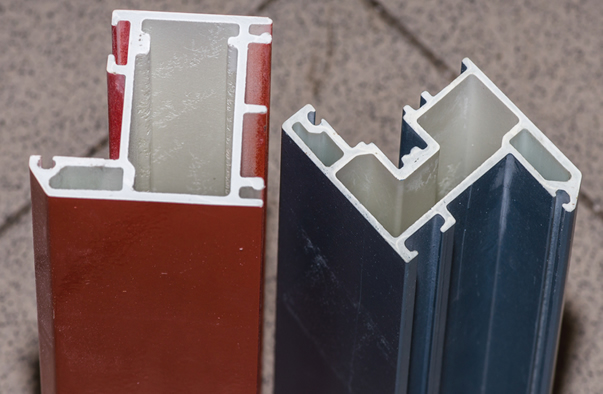
An automated high-volume continuous process where glass roving is “pulled” through a heated die creating a profile shape.
Pultrusion is a continuous and highly automated process, that is cost-effective in high volume production runs of constant cross section parts. Pultruded standard shapes include I-beams, channels, angles, beams, rods, bars, tubing, and sheets and have penetrated virtually every market. The pultrusion process relies on a caterpillar tread-like puller system which pulls fiber through a catalyzed resin bath, and into a heated metal die. As the wetted fiber passes through the die (formed in the shape of the desired profile) it is compacted and cured. The cured profile is then cut to length with automated saws that are synchronized to the line speed.
Alternative wet-out systems inject the resin directly into the heated die and multiple fiber streams can be pultruded in a single die with several cavities. To form hollow or multiple-cell parts, the wetted fiber wraps around heated mandrels that extend through the die. If off-axis structural strength is required, mat and/or stitched fabrics may be folded into the material package before it enters the die. Pultrusion applications typically uses fiberglass and thermoset resins such as polyester, vinyl ester, epoxy, and phenolic. Carbon fiber and other knitted and hybrid reinforcements can also be used depending on the performance requirements of the end product.
Composites One has a team of dedicated Pultrusion experts who can help guide manufacturers from product selection to process know-how.