Open Molding
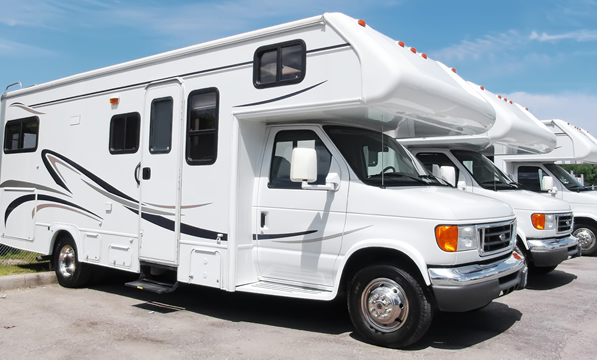
Open molding is a low cost and effective method to manufacture composites.
Open mold processes include, spray-up (chopping) and hand lay-up. This well established molding method is used to produce, boats, RV components, truck cabs and fenders, spas, tubs, showers, and other fiberglass composite products. In this process, a single-sided mold is used that acts as the form and cosmetic surface of the part. Gel coat is applied to the prepared mold surface. Reinforcements are then applied either by hand and then wet-out with catalyzed resin, or in the spray-up process where catalyzed resin and chopped fiberglass are sprayed onto the previously gel coated surface. Additional layers of laminate are added to build thickness and strength as desired. Air is then rolled out of the laminate by hand and the part is left to cure. In addition to reinforcements, low density core materials such as balsa wood, foam, or honeycomb can be added to stiffen the laminate without adding significant weight.
Open molding is the most flexible of all composite fabrication processes as part size and design options are virtually limitless. Typically, the open molding process is used for a large size range of products that cannot be produced in more automated processes, or for parts that are produced in low volumes that cannot justify the higher mold costs of automated processes.
Composites One has everything a manufacturer needs for the hand lay-up and spray-up processes. Gel coat, a variety of fiberglass reinforcement, catalyst, resin and equipment are all readily available from the top suppliers, and our technical support team is on-hand to assist with process questions and applications support.