Closed Molding
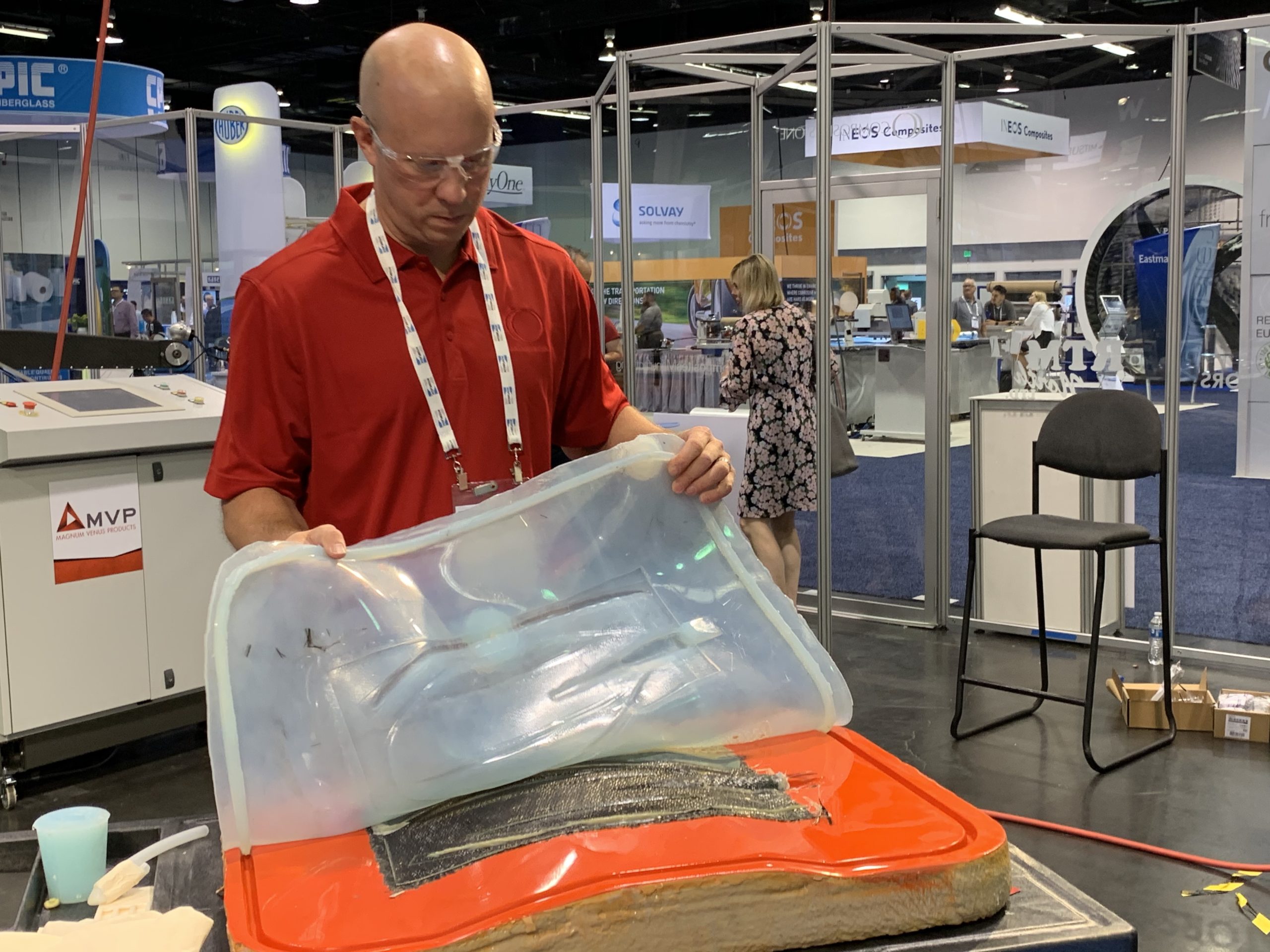
Closed mold processes such as Light Resin Transfer Molding (LRTM), Reusable Bag Molding (RSBM) and Vacuum Infusion Process (VIP) are used to produce precision parts at lower costs for a variety of applications. Typically, traditional composite tooling is used for the rigid base (or “A” side mold) in each these closed mold process, and several different materials may be used for the “B” side depending on the process. In closed molding, dry reinforcements are laid into the base mold, the mold is closed and resin is introduced into the closed cavity using a pressure pump or vacuum. When the laminate is cured the mold is opened and the part removed.
Compared to open molding, closed molding processes enable manufacturers to make better parts faster and more consistently, with less waste. Finished parts have better surface cosmetics, reducing the need for post work.
Because resin is cured in a closed mold system, there are significantly fewer emissions, helping manufacturers meet Federal and State emissions standards, while reducing the need for worker protective clothing and other PPE equipment. These processes are also less operator dependent compared to open molding, reduce labor and may require fewer molds reducing tooling costs.
Composites One along with the Closed Mold Alliance is the source for closed mold products, equipment, tooling and unmatched technical assistance.
Light Resin Transfer Molding (LRTM) is ideal for producing production parts with consistent quality and surface cosmetics.